Статьи о яхтинге
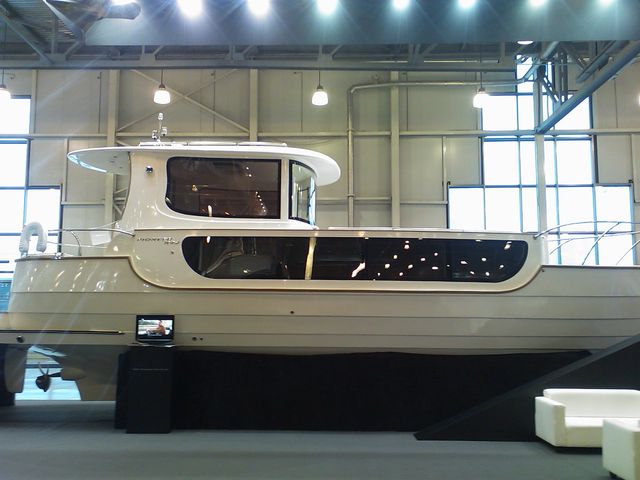
Технология изготовления яхт
В настоящее время яхты в основном изготавливаются из стеклопластика. Этот материал начал использоваться в судостроении ещё с сороковых годов 20-го века, но массовое применение он получил начиная с 70-х годов. Что же такое стеклопластик и почему он получил такое большое признание? По своей сути стеклопластик - это слои стеклоткани, пропитанные специальным связующим - эпоксидным, полиэфирным, винилэфирным и подобным им. Получающийся стеклопластик обладает отличными прочностными свойствами, не пропускает воду, имеет красивую гладкую поверхность, малый вес. Из стеклопластика можно легко изготавливать сложные криволинейные поверхности, что дает дизайнерам яхт большой простор для воображения. Гладкая поверхность из стеклопластика снижает сопротивление воды и позволяет инженерам рассчитывать и изготавливать корпуса яхт исходя из поставленных разнообразных задач. Стеклопластик с самого начала своего применения в судостроении был дешевле, чем дерево, не подвержен гниению. Некоторые корпуса яхт, построенные десятилетия назад, все ещё служат своим владельцам. Метод изготовления корпусов яхт позволяет изготавливать их в большом количестве, в промышленных масштабах.
В судостроении используют стеклоткань типа E - электротехническую ткань, иногда используют стеклоткань S типа - конструкционную, более прочную
Итак, стеклопластик- это стеклоткань, пропитанная сравнительно недорогими смолами. Зададимся вопросом: а почему тогда яхты не дешевеют, а качество их год от года падает? Почему теперь на ВСЕ массовые яхты гарантия на осмос (проникновение воды внутрь материала корпуса) не превышает 3 года, а на корпуса - 5 лет? Что же будет с яхтами после этого срока? С самого начала применения пластиков материал только дорожает. В условиях непрерывно растущей конкуренции, отягощенной еще и мировым экономическим кризисом, производители постепенно заменяют более качественные эпоксидные наполнители на более дешевые - полиэфирные. Для снижения себестоимости яхт начинают уменьшать толщину обшивки. Самую тонкую обшивку начинают делать с 80-х годов, но потом толщину все-таки немного увеличивают, начинают применять сэндвичевые многослойные материалы в конструкции палубы и бортов. Экономия и стремление уменьшить толщину слоя доходит до того, что на некоторых яхтах можно зайти внутрь корпуса и посмотреть сквозь обшивку - сильные лампы могут просвечивать сквозь неё! Для удешевления производства стали использовать не стеклоткани, а ровинг и стекломаты, уложенные попеременно, лишь накрытые сверху слоем стеклоткани, поскольку она имеет гладкую поверхность.
Стекломат - это материал, образованный из хаотически расположенных стеклянных волокон, применятеся в основном в виде наполнителя, поскольку не обладает достаточной прочностью. Тканый ровинг - это тяжелая грубая ткань из сплетенных стекловолокон. Однако, не смотря на такие жертвы, стоимость яхт все-таки значительно не падает. В чем же тут дело? На самом деле, большая часть затрат на создание яхты - это человеческий труд. Производство яхт в силу своей специфики остается ручным делом до сих пор, несмотря на все технические новшества. А иногда именно в силу применения этих новшеств и специфики производства стеклопластика требуется весьма квалифицированный труд.
Для изготовления корпусов яхт применяются несколько различных методов производства. Еще раз повторим, все они касаются различных технологий пропитки и смешивания стеклотканей (или стекловолокон и связующего).
Первый метод - ручное формование
По этой технологии сначала изготавливается модель корпуса в натуральную величину, так называемый болван. Затем болван обклеивается стеклотканью, изготавливается матрица. Эта матрица снимается с болвана, и уже на матрицу вручную укладываются несколько слоев стеклоткани и пропитываются связующим – полиэфирным, феноло-формальдегидным или эпоксидным. Слои стеклоткани раскатываются вручную валиком.
Ручное формование с использованием стекломатов
Одним из технологических этапов является ваккумная инфузия, когда уложенные слои из стеклоткани с пропиткой покрывают герметичным мешком, к которому присоединены множество трубок, отсасывающих воздух и создающих разрежение. При этом слои стеклоткани сильнее прижимаются друг к другу, удаляются излишки смолы, и ткань пропитывается более равномерно. Технология требует высококвалифицированного труда, ведь плохо уложенные слои и плохая пропитка может ускорить процессы осмоса (проникновения воды в материал корпуса яхты) в несколько раз, из-за неоднородности материла также снизится и итоговая прочность яхты.
Это самый распространенный тип изготовления яхт, так изготавливаются небольшие яхты и яхты малыми партиями. Важный момент: пропитывать слои стеклоткани нужно непрерывно, так как возникающие первичные клеевые связи гораздо прочнее вторичных. При одновременной припитке нескольких слоев образуется монолитный материал, обладающий исключительной прочностью. Если стеклоткань пропитывается эпоксидными смолами, то в результате мы получим материал, сравнимый по прочности со сталью. Но и стоимость получившегося материала довольно высока.
Применение вакуума при изготовлении пластиковых яхт
Напыление
При использовании технологии напыления смесь из стекловолокон и связующего из автомата распыляется на матрицу. В этом случае ручного труда немного, однако создаваемый корпус по своим прочностным характеристикам отличается от корпуса, где применяется листы стеклоткани. В настоящее время из-за низкой итоговой прочности корпуса этот метод почти не используется. Методом напыления изготавливают большие корпуса большой толщины, а также небольшие швертботы, где прочностные характеристики не так критичны, как для других типов яхт.
Инжекция смолы в закрытую форму
В этом случае требуется большие финансовые вложения в производство, ведь нужно изготовить две матрицы, точнее, матрицу и пуансон. Между ними укладываются слои сухой и предварительно раскроенной стеклоткани и подается под давлением связующее. И в этом случае не удастся полностью избежать ручного труда, ведь нужно предварительно раскроить ткань, уложить её и затем следить за точностью технологического процесса. Важное замечание: при применении всех приведенных методов нужно точно соблюдать температурный режим, следует точно соблюдать время пропитки. Это связано с происходящими химическими процессами в связующем – смоле. Некоторое время она находится в жидком состоянии, после чего сильно густеет и в дальнейшем уже плохо пропитывает слои стеклоткани – в результате может нарушиться технология изготовления материала.
Метод предварительной прокладки - Sheet mould compound
Следующая технология, по версии их создателей, призвана облегчить труд рабочих. Предварительно создается готовый материал - проложенные не до конца отвержденной смолой слои стеклоткани - sheet mould compound ( SMC). Для этого в наполнитель вводят разнообразные присадки. Слои такой ткани раскраиваются, укладываются в форму и прессуются при температуре примерно в 150 градусов, именно в это время и происходит пропитка слоев. Минус такого подхода – в постепенном изменении свойств смолы при долгом или неправильном хранении листового материала. Конструкторская мысль пошла затем ещё дальше, и теперь существует материал, представляющий из себя смесь стекловолокон и наполнителя. Этот материал, а вернее своеобразная паста, называемая bulk mould compound (BMC) помещается между двух металлических матриц и прессуется при давлении от 30 атмосфер и выше при температуре от 100 до 160 градусов. Стоимость создания металлических матриц и большого по размерам оборудования, позволяющее создавать повышенное давление при высокой температуре, могут позволить себе не все даже крупные судоверфи.
Итак, что мы видим? Для изготовления пластиковых корпусов яхт требуется достаточно большая предварительная подготовка: помимо точного инженерного расчета корпуса и создания привлекательного вида (расходы на дизайнеров) требуется создать полноразмерный болван, а затем и матрицу, с которой собственно и будет вестись формование будущих корпусов. Далее для изготовления яхт требуется либо высококвалифицированный ручной труд, либо такие дорогостоящие автоматизированные технологии, которые по финансовым затратам сопоставимы с ручным трудом, а то и превосходят его. Есть забавные факты, когда для создания небольшого швертбота при "высокотехнологичном" методе высокотемпературного формования в закрытой матрице потребовалось участие почти 10 человек, а чуть за большее время такой же по размерам швертбот мог изготовить один человек методом ручного формования.
Видны непроклеи стеклоткани на корпусе моторной яхты. Корпуса яхт с такими дефектами, вызванными неквалифицированной работой, прослужат недолго
"Сэндвичевые" материалы
С развитием космической отрасли появились многослойные высокотехнологичные структуры, где слои выполнены из разных материалов, - так называемые сэндвичи. Сэндвичи из нескольких слоев обладают легким весом, хорошими прочностными характеристиками. Эти инновационные материалы сразу привлекли внимание яхтостроителей. К этому времени уменьшать слой стеклопластика стало уже некуда. Палуба, изготовленная из цельного стеклопластика приемлемой толщины для прочности всей конструкции, попросту прогибается под ногами. Утолщение же слоя ведет к лишнему расходу материала и удорожанию яхты. Поэтому применение сэндвичей сразу решило эти проблемы. Технологи вернулись к испытанному материалу – бальсе. Это долго не гниющее, легкое дерево заключается между двух слоев пластика. Получается композитный материал, обеспечивающий приемлемую толщину, легкость и прочность конструкции яхты. Однако и тут есть сложности. Применять в качестве наполнителя бальсу в сэндвиче имеет смысл только в палубных конструкциях, так как бальса - органический материал и при попадании воды внутрь композита постепенно гниет. Палубу просверливают во множестве мест для установки релингов, люков и других приспособлений. Вода имеет массу возможностей проникнуть внутрь слоя. Постепенно материал разрушается и теряет свое преимущество. Применение бальсы как наполнителя в материале, который будет использоваться ниже ватерлинии, вообще нежелательно: вода будет просачиваться внутрь сэндвича под влиянием осмоса, по микропорам, постепенно разрушая бальсу. Кроме того, существует опасность плохого соединения бальсы со слоями стеклопластика. Это возможно при нарушении технологического процесса при применении неквалифицированного персонала.
При повреждениях обшивки видно, что наполнитель сэндвича CoreMat попросту не приклеен к к стеклоткани. Это вызвано только непрофессиональной работой при изготовлении яхты
После бальсы внимание яхтостроителей привлекли и другие материалы. Самый распространенный сейчас наполнитель в сэндвиче – пенопласт. Минусы: пенопласт выделяет вредные вещества – стирол, если его оставить на солнце, то через некоторое время он испарится, при большой температуре он плавится и горит с выделением вредных веществ. Рассчитать итоговую прочность композита с пенопластом достаточно сложно, поэтому неизвестной становится и итоговая прочность корпуса яхты.
В качестве наполнителя можно использовать также очень легкие сотовые структуры. Эти материалы по праву называют инновационными, их использование требует очень высококвалифицированного персонала. Если при ручной формовке стеклопластика небольшие огрехи при изготовлении всего лишь увеличат осмос и уменьшат время гарантии корпуса, то в случае сэндвича из сотовых структур ошибка при изготовлении может дорого стоить, – итоговая прочность резко уменьшится. Даже при небольшом ударе корпус из такого композитного материала необратимо разрушается.
В настоящее время наилучшими свойствами обладает композитный материал, образованный из стеклоткани снаружи и кевлара внутри. Однако некоторые современные яхты высокого класса, такие например, как Oyster, по прежнему изготавливаются из цельного стеклопластика, причем корпус ниже ватерлинии делается достаточно толстым.